While the fluid power industry has long met the needs of various industrial sectors, more environmentally friendly alternatives like electrification threaten to replace it. In the eyes of many industry professionals, it is time for a change. How will embracing emerging sustainability trends shape the future of hydraulics and pneumatics?
The State of Sustainability in the Fluid Power Industry
Although fluid power systems have done their jobs well for decades, discussions about change have become front and center in the industry. In recent years, regulators, business leaders and the general public have scrutinized various issues — oil leakage causing environmental damage, operations producing greenhouse gas emissions and nitrogen pollution causing biodiversity loss.
One of the main reasons professionals within the fluid power industry seek sustainability is government regulation. While greenhouse gas reductions and energy savings are leading drivers, agencies also regulate environmental hazards that have gone unnoticed for years. For instance, new rules targeting per- and polyfluoroalkyl substances (PFAS) are emerging.
Anionic PFAS — forever chemicals — are present in motors, seals and lines. They are widely used as additives in hydraulic fluids and cables to suppress corrosion, grant temperature resistance or prevent stress cracks from forming. Professionals must reimagine fluid power design to comply with various incoming regulations.
Of course, utility companies also seek to cushion their bottom lines or gain enough financial flexibility to take risks. As the industry evolves, exploring emerging trends can grant them a competitive advantage. At the very least, updating legacy devices is beneficial. Whatever their reasons, progress is already underway to make this industry more sustainable.
The Synergy Between Fluid Power and Sustainability
Industry professionals must optimize fluid power systems to comply with emerging regulations and shrink their carbon footprint. By increasing efficiency, reducing weight, and using better materials, they inadvertently improve performance and lessen space envelope restrictions. These gains enable machinery compaction. At the very least, they offer greater flexibility.
Leaders who deploy the latest monitoring technologies or leverage aspects of electrification can increase system longevity by reducing component degradation. Knowing precisely when to replace or repair valves, filters, actuators, fluid, compressors or cylinders reduces wear on adjacent parts, extending the equipment’s life span.
These performance gains translate to reduced costs. Energy consumption accounts for around 45% of the total cost in fluid hydraulics, while operation, maintenance and repair combined contribute 30%. As systems become more energy-efficient and require less maintenance, utility companies save a significant amount of money.
How Leaders Can Incorporate Sustainable Technology
There are several impactful ways leaders in the fluid power industry can embrace sustainability.
-
Leveraging Biodegradable Fluids
Biodegradable fluids are non-toxic, plant-based substances designed for high-pressure industrial applications. They reduce operation-related greenhouse gas emissions and mitigate environmental damage caused by leakage. In the hydraulics market, just 14% of oils used are bio-based. While this is still an emerging market, it has significant potential.
-
Integrating Smart Technologies
In electrified systems, the electronic control converts input to optimize operation. It enables the deployment of internet-connected sensors, allowing operators to monitor performance in real time. This way, they can prevent compressed air leaks or iden
Intelligent devices can set speed, velocity, pressure and flow to improve sustainability. For instance, a neural network model predictive control that uses a fully open flow control valve demonstrates a 15.35% energy consumption reduction under no load and a 9% reduction under 7.5 megapascals. It also lowers the average operating temperature by 10%.
-
Conserving Fluid With Recycling
Recycling to conserve fluid is a resource-efficient waste-reduction method that requires minimal upfront investments or aftermarket additions. Select services can re-refine oil or internal lubricants for repeated hydraulic and pneumatic use. A bonus is that utility companies save money, cushioning their bottom lines.
-
Optimizing for Energy Efficiency
Many of today’s fluid power devices waste energy — and a simple redesign is the solution. Take pneumatics, for example. Compressed air accounts for 78% of this system’s lifetime energy costs. Design improvements could reduce power consumption by 50% to 70%. Optimizing via weight reduction or new material use could substantially increase efficiency.
-
Leveraging Variable Speed Drives
On average, traditional fixed-speed pumps waste 20% to 80% of the power they consume. While some losses are unavoidable, reducing motor speed when full flow isn’t needed can improve efficiency. With a variable speed drive, energy savings reach 40% to 80%. Moreover, the machine runs substantially cooler and experiences no throttling losses.
How Sustainability Efforts Will Impact Future Systems
Sustainability efforts will permanently influence how engineers approach technical drawings. In one survey, 78% of respondents said sustainability influenced their hydraulic or pneumatic designs, with 35.85% changing 21% or more of their system’s structure. This figure will rise as development evolves and more cost-effective avenues are revealed.
Decision-makers should consider the return on investment and payback periods before they commit to any measure. They must know how soon their efforts will pay off to understand which approach is optimal. Even if they can afford to lose funds, conducting feasibility, cost and risk assessments is wise.
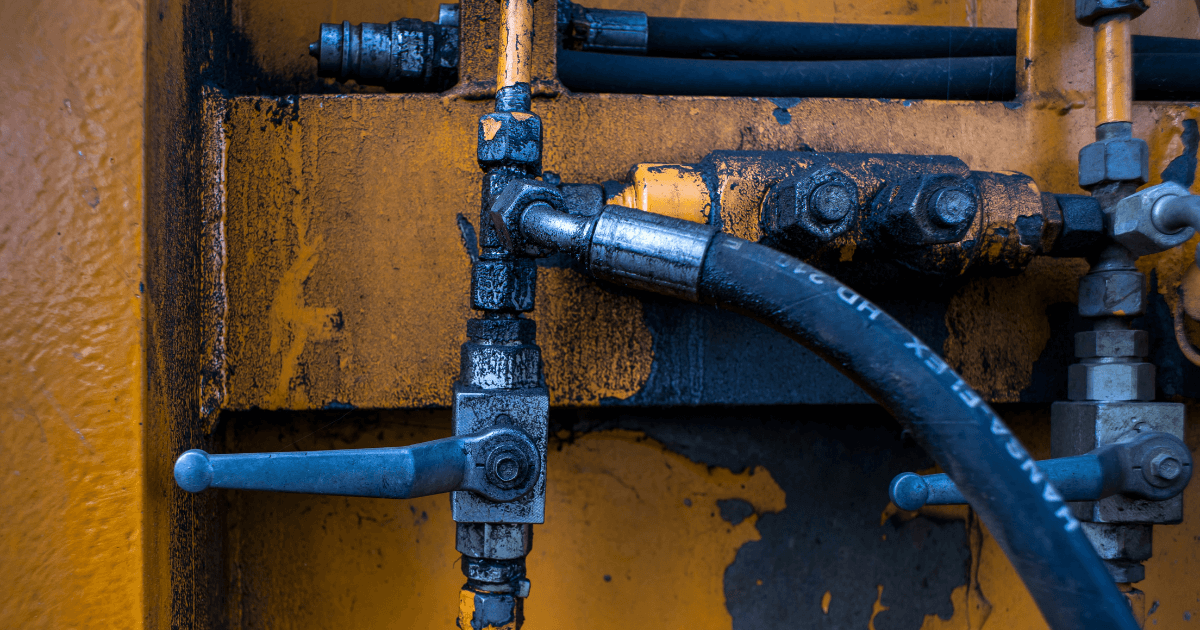
Soon, industry professionals will have to rethink upkeep. Whether they adopt electro-hydraulics or leverage biodegradable lubricants for pneumatic pumps, how they approach repairs will change. Even though their maintenance responsibilities will likely be less demanding and more cost-effective, they will require noticeably different steps.
While optimization and upgrades can extend equipment longevity, there will come a time when repairs are no longer enough. Leaders must be aware the end-of-life processes for their advanced designs will differ from traditional methods. For example, they may have to find a new servicer to dispose of biodegradable hydraulic oils.
Looking to the Fluid Power Industry’s Sustainable Future
As research and development progress, the design of hydraulics and pneumatics will evolve. No one can say with certainty whether these advancements will result in renewed interest in compaction, renewable energy or electrification. However, there will likely be a cross-over between adjacent fields.
Ideally, industry professionals’ sustainability efforts should align hydraulics and pneumatics with electrification. While these technologies don’t necessarily need to compete — fluid power is ingrained in various industries, so it will stay a staple for decades — advancement will help companies remain competitive with those who upgrade